Traditionally, there has been an enforced battery limit between shore based bulk materials handling infrastructure and vessel borne operations. AMH’s expansion into this market has required the development of key partnerships with various local and international transhipment companies to service the Australian Transhipment market.
AMH’s distinct competitive advantage draws from years of hands-on bulk materials handling experience stretching from the head end mining operations to the final outloading operations at the port (Pit to Port). Over the years, AMH has further developed inhouse capability to design, manufacture, commission and support in maintaining our own proprietary material handling systems, inclusive of shore-based shiploaders and stockyard machines.
Our tailored transhipment bulk materials handling plants combined with forward thinking self-propelled vessel designs from our shipping partners, are optimally positioned for the unique requirements of the Australian Transhipment Market, servicing mining projects ranging from 2.5 Mtpa to 45 Mtpa.
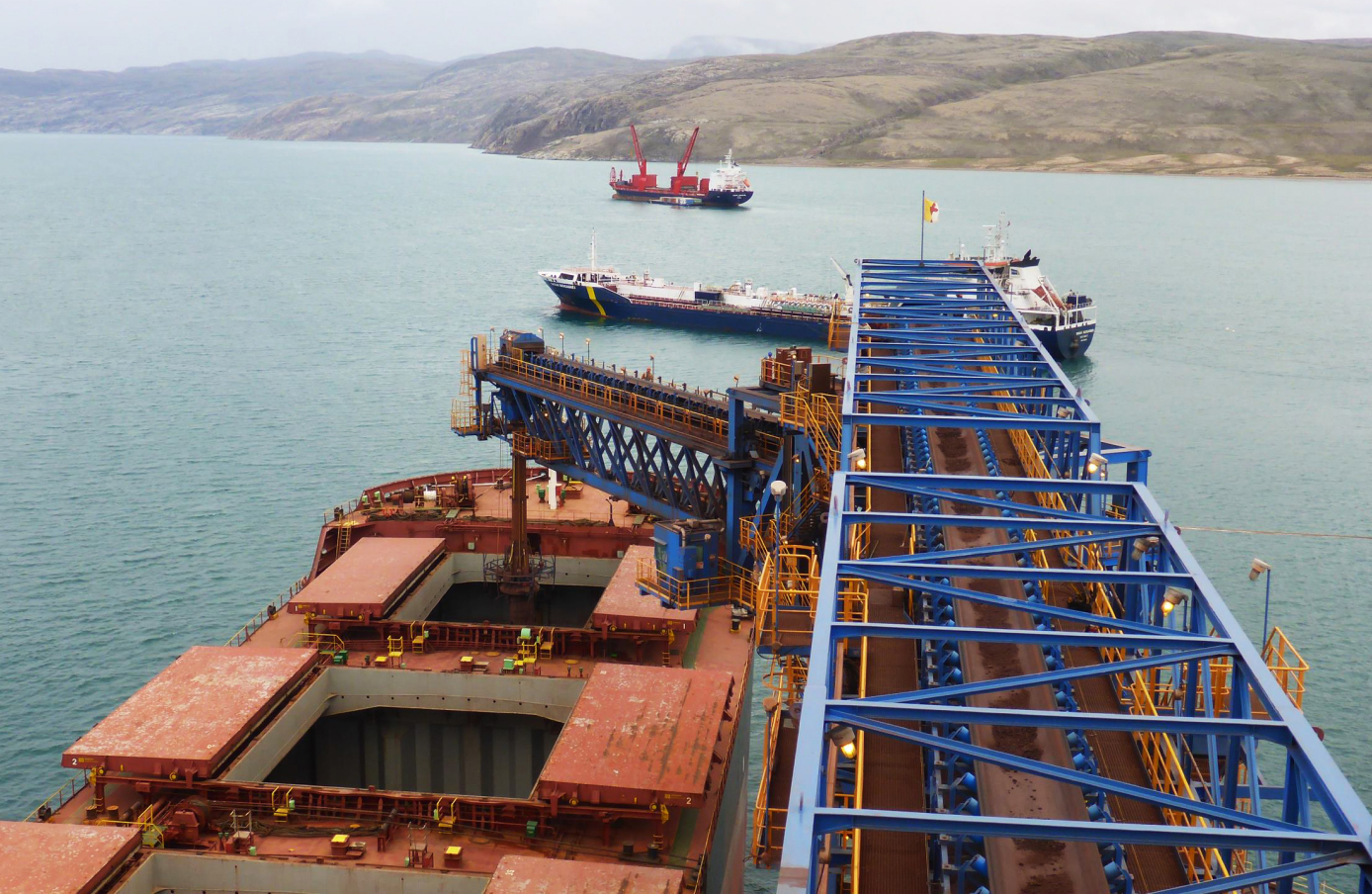
AMH’s collaboration with experienced transhipment companies additionally provides a viable and more sustainable alternative to traditional tug and barge operations for smaller mining projects, at a competitive price point.
Leveraging economies of scale by loading larger vessels offshore, including up to Cape Size vessels, at the required transhipment rates is now feasible for smaller mining projects. Our proprietary technology can achieve both transhipment and load-out rates ranging from 3,500 Mtph to 12,000 Mtpa (Nominal), with increased Mtbf and is less susceptible to wear and corrosion.
AMH’s transhipment bulk materials handling plants are up to 50% lighter when compared to traditional transhipment material handling plants due to our innovative designs and use of lightweight, corrosion resistant materials.
Key components are locally manufactured meaning local support is readily available and all fully compliant with the relevant Australian Standards. Lighter material handling plants further mitigate (or ideally eliminate) the extent of dredging required, as well as laden draft restrictions limiting TSV DWT capacity, releasing previous constraints on annual throughput.
Various transhipment bulk materials handling plant configurations are available for selection, enabling transhipment of multiple commodities at efficient throughput rates. AMH’s transhipment value chain designs additionally allow for up-stream and down-stream savings through integration with the land and wharf-based infrastructure. Further, through reducing OGV lay days due to optimal loadout configurations on board the TSV, operations are able to minimise shore-based CAPEX and OPEX spend due to our inherent efficiency gains and cycle time reductions.
Drawing from our extensive bulk materials handling experience and extending into the vessel borne TSV operations (“Pit to Hold” Value Chain), AMH’s transhipment material handling plants are more easily maintainable, with adequate redundancy in design to minimise risks relating to single points of failure during both load-out and transhipment operations.
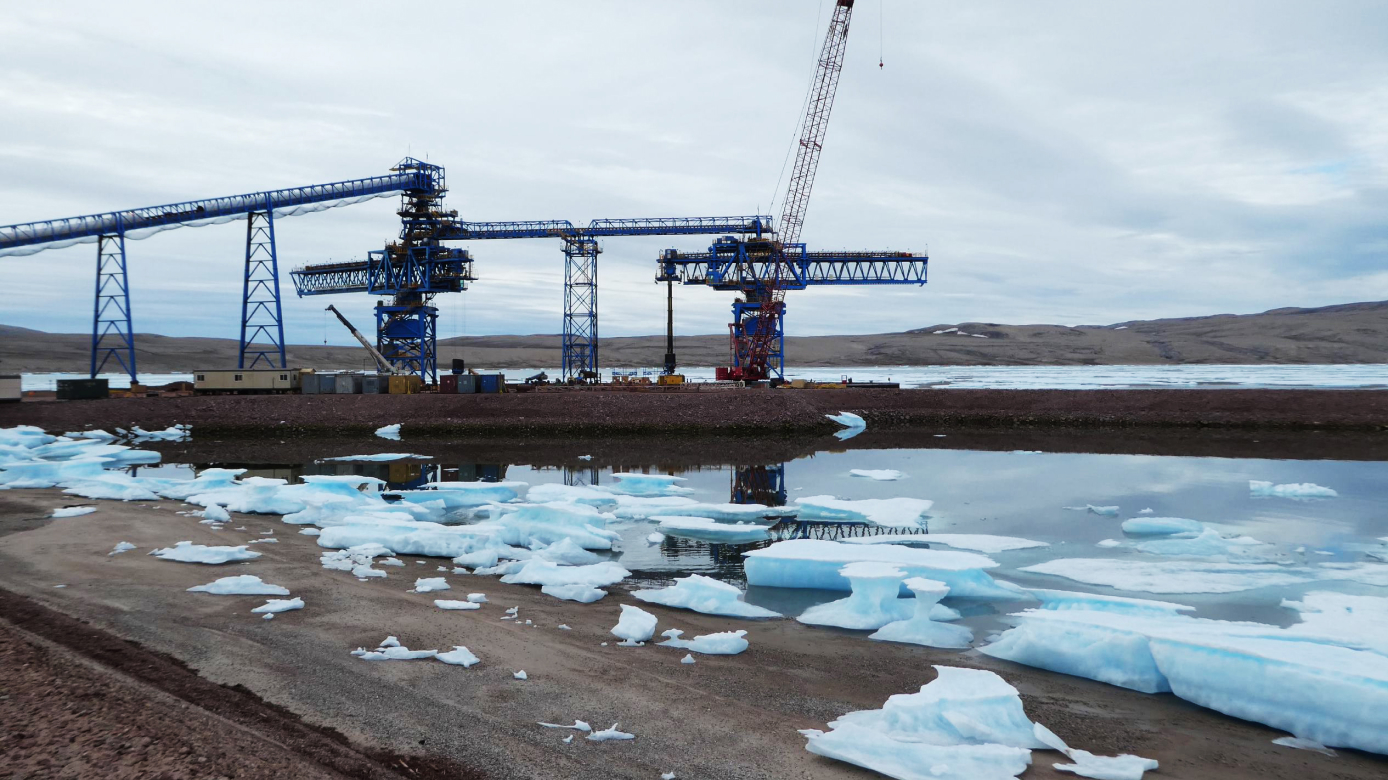
Each transhipment material handling plant is modular in design and manufacture and is therefore scalable across various transhipment vessel sizes ranging from 5,000 dwt to 30,000 dwt vessels, and even up to 60,000 dwt.
Utilising cutting edge technology, AMH’s transhipment bulk materials handling systems further extend to include fixed mooring arrangements and single point loading systems, thereby reducing the need for stevedoring and berthing delays.
Our interlocking SCADA systems and proprietary HoloReality technology further enables the crew of the self-propelled, self-unloading vessel to operate the wharf based shiploader from the transhipment vessel’s bridge, further reducing the need for shore-based labour spend.